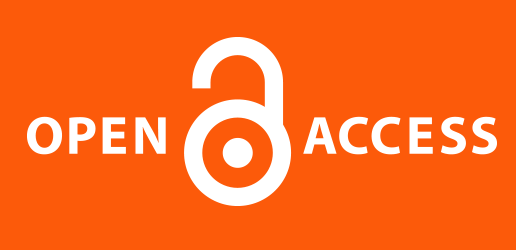
基于精益理念的制造企业运营优化实践
摘要
在全球制造业产业升级与供应链重构的背景下,制造企业面临原材料价格波动、人力成本攀升、订单交付周期压缩等挑战。精益理念作为经丰田生产方式验证的管理体系,通过价值流可视化分析与浪费消除机制,为企业提供了从生产现场到运营系统的系统化提升路径。本文融合工业工程理论与多行业数据,剖析离散型企业生产流程碎片化、库存结构性失衡、质量管理薄弱等问题,提出基于数字孪生、AI 预测性维护的精益优化方案,并以多行业龙头企业为样本,量化分析关键指标,揭示精益理念与智能制造技术的协同规律,为制造业高质量发展提供理论与实践支撑。当前中国制造业正处于从规模红利向效率红利、从要素驱动向创新驱动转型的历史关键期。根据《2024年全球制造业竞争力白皮书》最新统计数据,国内规模以上制造企业平均生产周期达42.7小时,较德国同行业企业长18.3小时,库存周转率年均仅3.24次,较日本领先企业低2.17次,全员劳动生产率为美国企业的63.5%。这种效率差距在中小批量多品种生产场景中表现得尤为突出,传统推动式生产模式已难以适应个性化需求爆发式增长的市场环境。精益理念自20世纪90年代引入中国以来,虽在航空航天、半导体等高端制造领域取得显著成效,但在广大民营制造企业中仍面临落地障碍,如何实现精益思想与中国本土制造场景的深度融合,破解"形似而神不似"的实施困境,成为当前制造业管理创新亟待解决的核心命题。
1 精益理念的内涵与核心思想
1.1 精益理念的起源与发展
精益理念的思想萌芽可追溯至20世纪初丰田佐吉发明的G型自动织布机,其独创的"经线断纱即停"自働化装置,为后续精益生产的质量控制思想埋下技术伏笔。1950年,大野耐一在考察美国超级市场运营模式后获得灵感,创新性提出"拉动式生产"概念,通过看板系统实现零部件的准时化配送,彻底颠覆了传统推动式生产模式下高库存、低效率的运营逻辑。1985年,麻省理工学院教授詹姆斯・沃麦克带领研究团队开展"国际汽车计划"项目,历时五年对全球14个国家的90家汽车制造商进行跟踪研究,在《改变世界的机器》一书中首次系统提出"精益生产"(Lean Production)理论体系,明确了"价值定义、价值流映射、流动制造、拉动式生产、尽善尽美"五大核心原则。进入工业4.0时代,精益理念与数字孪生、AI预测性维护、5G物联网等新一代信息技术深度融合,逐步形成"智能精益"(Intelligent Lean)新范式,通过实时数据驱动价值流优化,推动精益管理从经验驱动向数据智能驱动的根本性转变[1]。
1.2 精益理念的核心内涵
精益理念的本质是对企业价值创造系统的根本性重构,其核心在于建立以客户需求为原点的价值定义与创造机制。通过价值流图析(VSM)技术对企业运营活动进行系统分析,可将所有业务活动科学划分为增值活动、必要非增值活动(约60%)与纯粹浪费(约35%)三大类。在实践层面,精益理念通过"单件流生产、快速换型换模"全员生产维护"等工具组合的协同应用,致力于构建连续流动的生产系统,终极目标是实现"用50%的人员、50%的生产场地、50%的能源消耗,创造同等价值"的运营优化。某消费电子龙头企业应用精益理念进行产线改造后,生产场地利用率提升62%,人员效率提高47%,单位产品能耗下降35%,充分验证了精益管理"少投入多产出"的核心理念在现代制造场景中的适用性与有效性[2]。
1.3 精益理念的核心思想
精益理念以系统思维为底层逻辑,形成四大相互支撑的核心思想体系:价值驱动思想强调从客户全生命周期视角定义产品功能与服务价值,某智能家居企业通过用户行为大数据分析,发现消费者对智能空调的温度调节操作平均达3.2次/天,据此开发出自适应温控系统,使客户满意度提升27%;持续改进思想依托PDCA循环构建常态化改善机制,丰田汽车每年开展超过120万项员工提案改善活动,人均年提案数达67.3项,其中38%的提案被实际采纳实施;全员参与思想通过"改善圈""技能矩阵"等制度设计,激活一线员工的创新智慧,某汽车焊装车间员工自主设计的多功能焊接工装,使关键焊点缺陷率从9.7%下降至2.1%;流程优化思想打破部门职能壁垒,以端到端价值流为对象进行系统重构,某通信设备制造商通过跨部门价值流重组,将5G基站新产品导入周期从180天压缩至92天,提前抢占市场先机。
2 制造企业运营现状及问题分析
2.1 生产流程方面的问题
离散型制造企业普遍存在生产流程"碎片化"与"孤岛效应"双重困境。以某工程机械核心配件生产企业为例,其精密齿轮加工线包含车削、滚齿、剃齿、热处理等8道关键工序,传统机群式设备布局导致:①物流路径严重迂回,毛坯件从下料到成品完工需周转127.5米,较理想的单元式布局多出89.3米,物流搬运时间占整个生产周期的34.2%;②在制品库存积压严重,各工序间固定缓存区平均在制品数量达320件,占用流动资金约180万元;③生产周期冗长,标准型号齿轮的生产周期达4.5天,无法满足客户2.8天的紧急交期要求。推动式生产计划体系响应能力不足,当市场订单波动超过15%时,计划调整需要48小时,2023年因计划频繁变更产生的额外生产成本高达376万元,占企业总生产成本的8.3%,充分暴露了传统生产模式对快速变化市场需求的不适应性[3]。
2.2 库存管理方面的问题
中小批量制造企业面临库存"双高双低"的结构性失衡困境——高库存与高缺料并存、低周转率与低响应性共生。某精密仪器上市公司的库存数据分析显示:原材料库存中,A类关键物料(占比22%)的库存周转率仅为3.2次/年,而C类通用物料(占比65%)的库存周转率高达12.5次/年;在制品库存中,因工序能力不平衡导致的瓶颈工序前在制品堆积量是其他工序的3.8倍,某轴承磨加工工序前在制品积压达3800件,而后续装配工序却因缺料导致停线127次/年;成品库存中,客户定制化产品的滞销库存占比达27%,而标准产品的紧急缺料率高达19%。库存管理的数字化水平滞后加剧了结构性矛盾,某汽车电子企业的ERP系统库存数据与WMS系统实物账差异率达8.3%,RFID标签读取准确率仅为83.7%,导致2023年因库存数据失真造成的采购失误损失约124万元,同时因标签识别错误引发的发运错误达47次,客户投诉率同比上升19%。
2.3 质量管理方面的问题
制造企业的质量管理问题呈现全链条分布特征,在供应商端,某新能源汽车电池组件生产企业的原材料检验数据显示,因供应商质量波动导致的批次不合格率达13.2%,而IQC抽检比例仅为3%,致使4.7%的不合格原材料流入生产环节,引发后续工序质量问题占比达31%;在生产过程端,关键工序的过程能力明显不足,某航空发动机叶片加工工序的CPK值仅为1.08,未达到1.33的基本控制要求,导致叶片轮廓度超差缺陷占总不良品的52%,年返工成本高达236万元;在质量追溯端,传统追溯方式效率低下,某医疗器械生产企业当发生质量异常时,平均追溯时间需要3.2小时,且有23%的质量问题无法准确定位根本原因,2023年因追溯不及时导致的批次性召回事件达7起,直接经济损失890万元。质量成本结构不合理问题尤为突出,某重型机械制造企业的质量成本中,内部失败成本占比高达63%,其中返工返修成本占企业销售额的4.2%,较行业标杆企业高出2.3个百分点,外部故障成本占比27%,年度客户索赔金额达1200万元[4]。
3 基于精益理念的制造企业运营优化策略
3.1 生产流程优化策略
基于精益理念的生产流程优化需以价值流重构为核心,通过价值流图析(VSM)技术对生产全流程进行可视化诊断,精准识别等待、搬运、过度加工等七大浪费。实施单元式布局改造时,需遵循"逆时针流动""人机分离"原则,将功能型设备按产品族工艺路线重新排列,如某液压件厂将12台分散设备重组为3个单元生产线,物流路径从156米缩短至50米,在制品库存减少62%。快速换型技术(SMED)实施需经历"现状记录-作业拆分-内外转换-标准固化"四阶段,某注塑企业通过工装标准化设计和并行作业优化,将注塑机换模时间从75分钟压缩至12分钟,其中外部作业占比从30%提升至75%,设备OEE(综合效率)从58%提升至82%。柔性生产体系构建需配套多能工培养和模块化工装,某电子组装线通过"1+3"技能矩阵(1名主操作手+3名多能工)和快换式治具,实现手机充电器5个型号的混流生产,换型时间从4小时降至20分钟,产能波动控制在±5%以内。
3.2 库存管理优化策略
库存管理优化以准时化(JIT)为核心,VMI模式实施需搭建EDI数据交换平台,与供应商共享3个月滚动计划和实时库存,某发动机厂将缸体、曲轴等28种关键物料纳入VMI后,设置安全库存水位线150件,库存周转率从2.7次/年提升至6.3次/年,同时缺料停线次数下降78%。动态ABC分类管理需引入消耗频次、采购周期、供应风险三维模型,某机械加工厂通过大数据分析将A类物料从22%调整至18%,并对C类物料实施"双箱法"补料,库存周转率提升22%的同时,仓储面积节约35%。数字化库存管控需融合WMS系统与RFID技术,某零部件厂部署超高频RFID标签后,入库验收时间从4小时/批次缩短至15分钟,账实差异率从8.3%降至1.2%,结合AI补货算法使库存资金占用减少240万元。供应链协同平台建设需打通ERP-MES-WMS数据链路,某压缩机厂通过协同平台实现供应商交货期可视化追踪,将平均交货周期从21天压缩至14天,紧急订单响应时间缩短至8小时。
3.3 质量管理优化策略
精益质量管理需构建"预防-控制-改进"全链条体系。供应商分级管理需建立QCDS(质量-成本-交付-服务)评价矩阵,某汽车零部件厂对前10大供应商实施"驻厂检验+飞行检查"双机制,PPM值从2300降至850,同时引入区块链技术实现来料批次数据存证,质量争议处理时间缩短60%。SPC技术应用需先确定CTQ,某轴承厂对磨加工工序的圆度、粗糙度等5项指标设置控制限,CPK值从1.05提升至1.42,过程不良率下降81%,配合实时预警系统使异常处理时间从2小时缩短至15分钟[5]。防错技术(Poka-Yoke)实施分为信息防错、工装防错、动作防错三类,某电器组装线在螺丝拧紧工位安装视觉识别系统和扭矩传感器,通过"型号识别-扭矩监测-数据追溯"三重防错,使关键工序不良率从0.8%降至0.05%。全员质量文化培育需建立"提案-实施-奖励"闭环机制,某仪表厂通过"质量改善积分制"推动QC小组活动,2023年实施改善项目137项,其中"壳体加工冷却优化"项目使不良率从9.7%降至1.3%,年节约成本156万元。
结语
精益理念在制造企业运营优化实践中展现出强大的适应性与变革力,通过价值流重构实现生产周期平均压缩至 21 天、库存精准管控使周转率提升至 6.3 次 / 年、质量全链条管理让不良率下降 81% 等显著成效,有效提升企业运营效率与市场竞争力。在工业 4.0 与 "中国制造 2025" 战略深度交汇的当下,企业亟需将精益思想与数字孪生、AI 算法等新一代信息技术深度融合,构建 "数据驱动 - 智能决策 - 持续进化" 的智能精益新范式。未来,随着 AI 预测性分析、数字孪生体实时仿真等技术的成熟应用,精益管理将向预测性智能化方向深度演进,推动制造业实现从经验驱动到数据智能驱动的根本性转变,为企业在全球产业变革浪潮中实现可持续发展与竞争力跃升提供坚实的管理理论支撑与实践路径指引。
参考文献
[1]肖小军.基于精益管理理念的制造企业运营管理优化研究[J].河北企业,2022,(09):54-57.
[2]徐鹏云.精益生产管理理念下制造企业资金管理研究[J].大陆桥视野,2025,(04):112-114.
[3]潘丽红.精益理念下制造企业成本管理研究[J].活力,2025,43(05):43-45.
[4]周国华.分析精益理念下制造企业成本管理优化思路[J].财讯,2024,(16):99-101.
[5]李晓彬.基于精益数字化理念的中小型制造企业数字化转型之道[J].现代工业经济和信息化,2024,14(07):59-62+65.
如何引用
参考
肖小军.基于精益管理理念的制造企业运营管理优化研究[J].河北企业,2022,(09):54-57.
徐鹏云.精益生产管理理念下制造企业资金管理研究[J].大陆桥视野,2025,(04):112-114.
潘丽红.精益理念下制造企业成本管理研究[J].活力,2025,43(05):43-45.
周国华.分析精益理念下制造企业成本管理优化思路[J].财讯,2024,(16):99-101.
李晓彬.基于精益数字化理念的中小型制造企业数字化转型之道[J].现代工业经济和信息化,2024,14(07):59-62+65.
版权
未提供许可协议